World-Class Conveyor Rollers, Conveyor Pulleys & Tube Fabrication Products
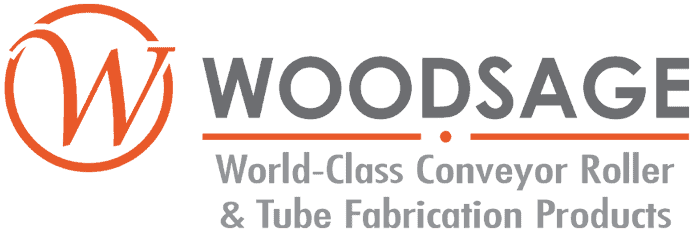
As a world-class supplier of conveyor system components and tube-based fabricated products, Woodsage can reduce, bend, expand, form, swage, spin, laser-cut, weld and machine to your exact specifications.
Through our ISO 9001:2015 certified manufacturing facility, Woodsage offers the shortest lead times and best on-time delivery rates in the industry.
Put the power and expertise of Woodsage to work on your next stainless or carbon tube-based project!

Conveyor Rollers
Woodsage has produced more than 1,000,000 rollers for material handling installations around the world.
Our conveyor roller component lines include:
- Tapered Rollers
- Grooved Straight Rollers
- High-Speed Rollers
- Heavy-Duty Rollers
- Gravity Rollers
- Specialty Rollers
- CDLR Rollers
Tube Fabrication
Each year, Woodsage processes more than 3,000 miles of tubing. Woodsage can cut stainless or carbon tubes, round or bar, up to 6-inches in diameter.
Our tube fabricating services include:
- Holes
- Slots
- Copes
- True Miters Cuts
- Custom, Intricate Designs
(Including Logos) - Made in USA!
Exhaust Systems
Using a variety of manufacturing techniques, Woodsage makes after-market motorcycle and automotive exhaust system components:
Exhaust components include:
- Complete Muffler Assemblies
- Exhaust Header Tubes
- Heat Shields
- Baffles
- Inlets
- End Caps
- Catalytic Converters